The researcher can place the circuit near the microphone or a tape recorder as shown in Fig. 1, adding a new form of energy to the experiments. This energy can be modulated by the Voices (see authors note) and also combined by beat with the white noise needed for the experiments.
This article was originally published in my book Electronic Projects from The Next Dimension and indicated to be used in EVP experiments.
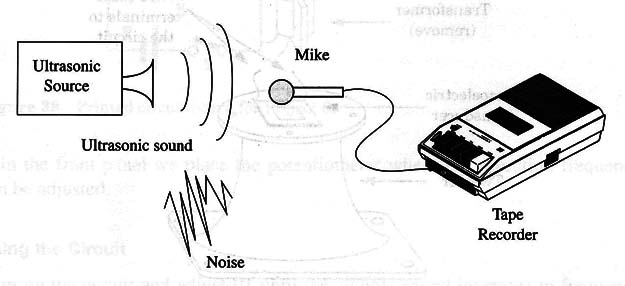
The experimenter can try several combinations of whitelpink noise generators and the ultrasonic generator to make these experiments. Two ultrasonic generators, operating at different frequencies, can be used to create beats for experiments involving EVP.
How It Works
The ultrasonic signal source is an oscillator based on one of the four Schmitt NAND gates of a CMOS 4093 IC. The frequency can be adjusted within a wide range of values by means of potentiometer P1.
With the values shown in the diagram, the circuit can produce ultrasounds in a range between 10,000 and 30,000 Hz. The audible part of the band is important, as it can be used to test circuit operation. The signals are amplified by the other three NAND gates wired as digital amplifiers.
For the transducer, we recommend the use of a piezoelectric tweeter. Many piezoelectric tweeters provide good performance when reproducing sounds between 18,000 and 22,000 Hz. However, to use the tweeter, some modifications must be made to this component.
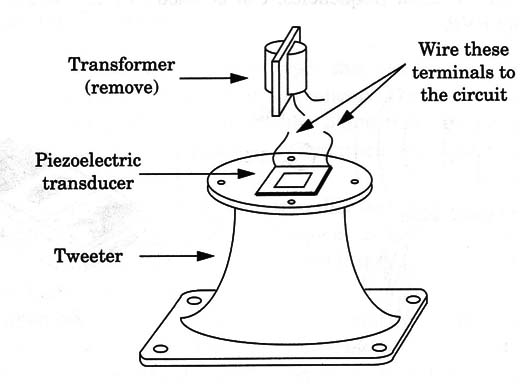
The tweeter (high-frequency loudspeaker) is a low-impedance device, due to the presence of a small transformer inside.
As our circuit has a high-impedance output, it is necessary to remove the small transformer inside the tweeter as shown in Fig. 2. Accessing the piezoelectric ceramic transducer, we can wire it directly to the output of our circuit.
The circuit can provide a few milliwatts of ultrasonics when powered from AA cells or a 9 V battery. This power is enough to conduct experiments in which it is placed near the microphone.
Assembly
The complete circuit of the low-power ultrasonic source is shown in Fig. 3.
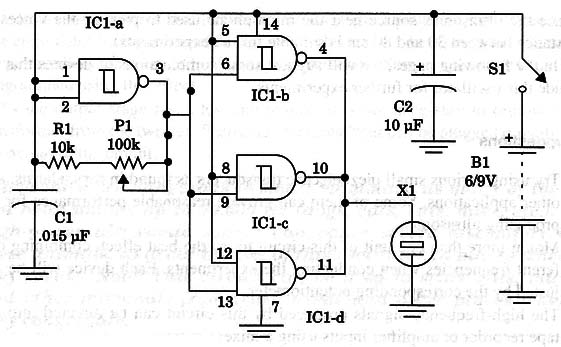
A small printed circuit board is used to mount the components. The layout for this printed circuit board is suggested in Fig. 4.
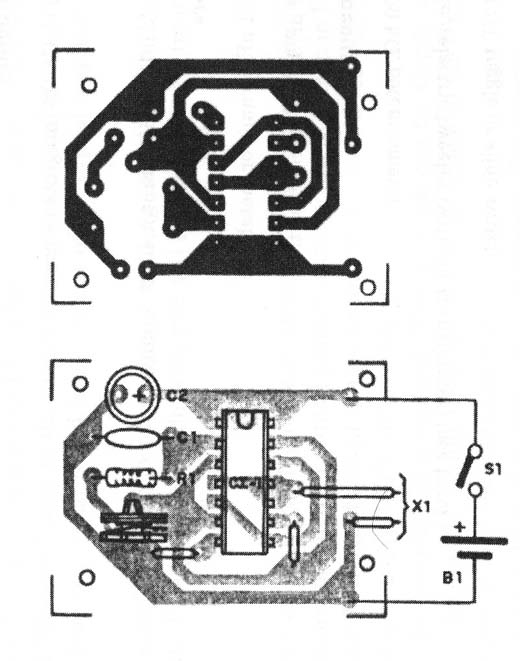
The compo- nents, including the piezoelectric tweeter and the battery holder, can be housed in a small plastic box.
In the front panel we place the potentiometer where the operation frequency can be adjusted.
Using the Circuit
Turn on the circuit and adjust Pl until the audible sound increases in frequency and then disappears. This indicates that ultrasonics are being produced.
Then place the ultrasonics source near the microphone used to pick up the voices (a distance between 30 and 80 cm is suitable for the experiments).
Suggestions
Try using various small piezoelectric transducers as found in toys, alarms, and other applications. Some of them can provide reasonable performance for reproducing Ultrasonics.
Mount more than one unit of this circuit to try the beat effect, combining different frequencies when conducting the experiments. Each device will be adjusted by the corresponding potentiometer.
The high-frequency signals produced by this circuit can be directed into the tape recorder or amplifier inputs using a mixer.
Semiconductors
IC1 - 4093, CMOS integrated circuit
Resistor
R1 - 10 k ohm, 1/8 W, 5% - brown, black, orange
Capacitors
C1 - 0.01 pF, ceramic or metal film
C2 - 10 µF, 12 WVdc, electrolytic
Miscellaneous
P1 - 100 k ohm, potentiometer
X1 - Piezoelectric tweeter (Without transformer) (see text)
S1- SPST, toggle or slide switch
B1 - 6 to 9 V, 4 AA cells or 9 V battery
Printed circuit board, battery clip or holder, plastic box, knob for P1, wires, solder, etc.