Note: the author originally published this article in one of the brazilian magazines he had worked and after it was included in his book Mechatronics sourcebook.
As we said, if a piece of iron is placed near the solenoid, it is pulled by the magnetic forces generated by the coil, as shown by figure 1.
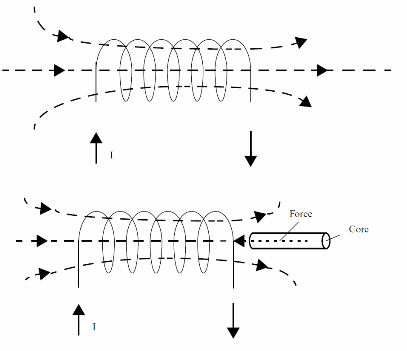
The force pulling the core depends on several factors.
a. The current passing through the coil
b. The number of turns in the coil
c. The material of the core
d. The stroke (distance the core moves)
Common solenoids powered from 3 to 48 VDC supplies have currents in the range of 50 mA to 2 A. Some solenoids can release several kilograms of force when activated. Solenoids can also be powered from AC supplies.
TYPES OF SOLENOIDS
Figure 2 shows some of the main types of solenoids, as listed below.
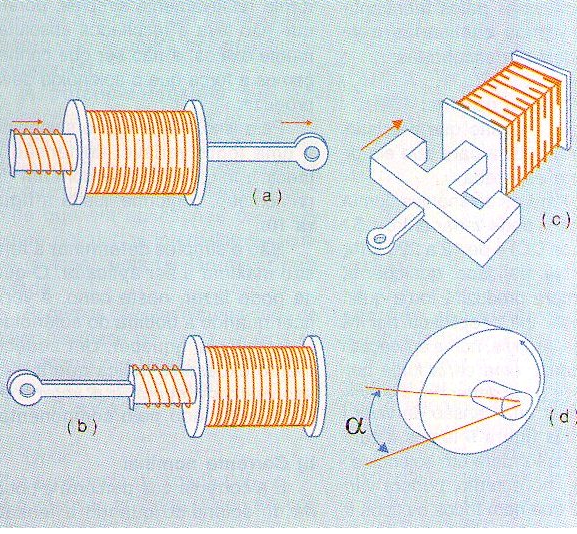
a. Linear laminated pull
b. Linear tubular, push
c. Linear tubular, pull
d. Rotary
USING THE SOLENOID
Solenoids are used when only a short push or pull is needed, moving the core a short distance as shown in figure.3.
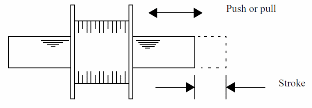
You simply have to connect the solenoid to the piece to be moved, keeping in mind the required force and displacement of the core.
To meet the requirements of various practical applications for solenoids, they are available in different shapes and sizes.
Figure 4 shows some applications for the solenoids in mechatronics as follows:
a. Push action
b. Pull action
c. Using a lever
d. Using a linear solenoid to obtain rotary motion
e. Rotary solenoid
f. Double action
g. Projecting objects
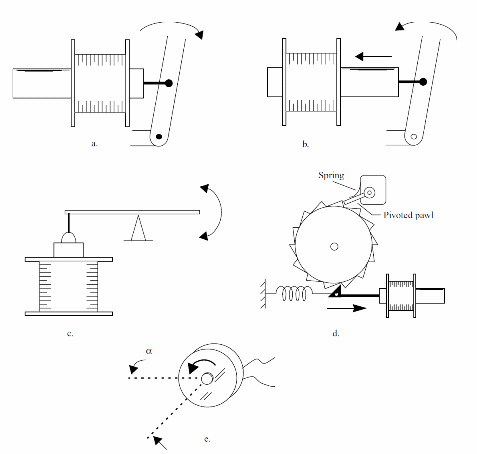
CHARACTERISTICS
The main specifications ofa solenoid are as described below.
a. the Force/Stroke created. The force created by the plunger ofa solenoid is a function of the applied voltage (and the current flowing through the device). The nominal force is the force generated when the nominal voltage is applied. This force is normally expressed in newtons (N) for linear solenoids and in terms of torque expressed in newton-meters (Nm) for rotary solenoids. Other factors that influence the solenoid force/ stroke relationship are temperature and duty cycle.
b. The nominal voltage (Vn). The voltage that may be applied to the coil of a solenoid to produce the nominal force is the nominal voltage or operating volt-age. Common types can have nominal voltage specifications between 3 and 48 V.
c. Type voltage. Solenoids can be powered from AC or DC sources. AC solenoids have a different construction, since they must include resources to damp the vibrations caused by the changes in the direction of the current flowing through the coil winding.
d. The nominal current (In). This refers to the current that flows through the coil when the nominal voltage is applied. This current can vary between 100 mA and several amperes for common solenoids.
e. The nominal resistance (Rn). Nominal resistance is the resistance of the coil winding. This resistance, along with the applied voltage, will determine the nominal current of a solenoid. For common types, this resistance varies from a fraction of an ohm to several hundred Ω.
f. Maximum dissipation power (PH). Heat is generated in the coil of a solenoid when current flows through it. If a solenoid overheats, it can burn. An important specification of the solenoid is its maximum dissipation power This power can range from several milliwatts to several watts. Below, we show how to calculate this power when it is not provided by the manufacturer.
Other characteristics of importance for some applications are the mechanical life and the force/ stroke curves.
Formulas:
The nominal voltage, nominal current, and the nominal resistances are interdependent. If any two of them are known, the third can be calculated using Ohm’s law.
The following are useful formulas for calculating these values.
a. Determining the resistance when the voltage and current are known:
R = V/I (6.1)
b. Determining the current when voltage and resistance are known:
I = V/R (6.2)
c. Determining the voltage when the current and resistance are known:
V = R x I (6.3)
where
R = coil resistance (ohm)
V= nominal voltage (V)
I = nominal current (A)
a. Continuous operation. The power dissipated by the coil of a solenoid when powered with the nominal voltage is calculated by the next formula:
P= V x I = R x I2 = V2 / R
where
P = power dissipated by the solenoid (W)
R = coil resistance (ohm)
V= nominal voltage (V)
I = nominal current (A)
b. Pulsed operation (considering the duty cycle).
P = V x I x DT / 100
Where:
P = power dissipated by the solenoid (W)
R = coil resistance (ohm)
V= nominal voltage (V)
I = nominal current (A)
DT= duty cycle (%)
In any application, P must be lower than Pd (the maximum dissipation power) to avoid overheating the solenoid.
Obs: Since, in many applications, the solenoid is activated for only a short time,
the maximum dissipation power is not necessarily an absolute limit.
DUTY CYCLE
The duty cycle of a solenoid is the ratio of the time on to the total operational cycle time. For optimal operation, the duty cycle should be minimized.
Formula:
The duty cycle can be expressed as
DT = 100 x (Ton / (Ton + Toff) )
where
DT = duty cycle in percent
Ton = time the solenoid is on
T off = time the solenoid is off
Obs.: The duty cycle also determines the amount of power dissipated by the solenoid in a particular application.