An unprecedented solution takes advantage of the vibration of motors, moving parts or oscillations to generate sufficient energy for the system of motion sensing or rotation.
The system, based on a piezoelectric transducer, can generate enough power to power a small wireless sensor system capable of sending information to a receiver connected to a computer or other control equipment.
The monitoring of rotors, gears and other equipment that has rotating parts such as fans, pumps and compressors presents drawbacks that require special care of the designers. In fact, a wireless system to monitor these devices requires not only the use of batteries (consisting of a constant maintenance element), but also special circuits that receive the signals from the sensors and convert them to the digital form for transmission.
Perpetuum, a specialist in vibration energy solutions, has now developed a power-generating system for powering a wireless sensor system from the motor vibration or monitored system.
The device consists of a wireless vibration monitor for rotary systems, based on a company's PMG17 microgenerator. In this system, a piezoelectric transducer converts the vibration energy of the monitored device into electrical energy, which, in turn, feeds the whole circuit of sensing and wireless sending of the rotation or movement of the part. This eliminates the need for battery for the application.
The PMG17 micro generator is designed to operate primarily with alternating current motors that have a typical natural vibration that is twice the frequency of the network. With Vibrations as small as 25 mg (rms) in a 2 Hz range, the unit produces a minimum electrical power of 0.5 mW and can deliver up to 40 mW of power with higher Vibration levels.
The device that produces 22 Vac (peak-to-peak) output has a typical application circuit shown in Figure 1.
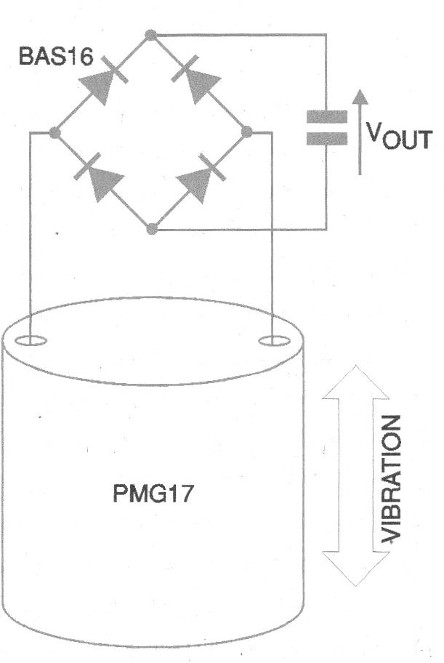
The PMG17-100 has operating levels in the 98-100 Hz frequency range and the PMG17-120 operates between 1 18 and 120 Hz, thus providing two design options.
In figure 2 we have the typical yield curve obtained as a function of frequency.
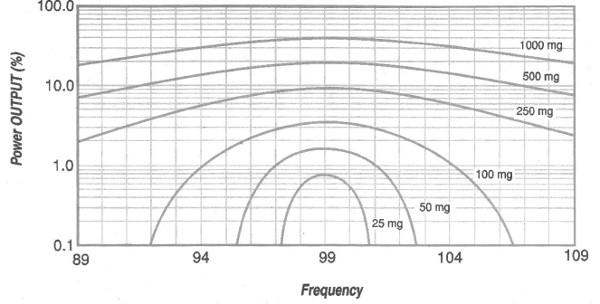
The power generated by this device allows data transfer at a rate of 6 kbytes per second by monitoring the device used at small intervals determined by programming.
The circuit is formed by a piezoelectric accelerometer that measures the vibration signal, a signal conditioning circuit, a microcontroller, a power conditioner, a radio transmitter, a power storage system and the PMG17 generator.
The accelerometer measures the vibration frequency (which depends on the mechanical construction of the system being monitored) as well as its speed of rotation, as well as the amplitude of the vibration. A switched source with more than 75% efficiency raises the power from 20 mJ to 27 mJ, thus charging a capacitor in a power conditioning circuit.
In this way, the AC energy produced in the generator is converted to the DC form.
In Figure 3 we see a block diagram showing the principle of complete operation of the wireless sensing system and without the use of batteries.
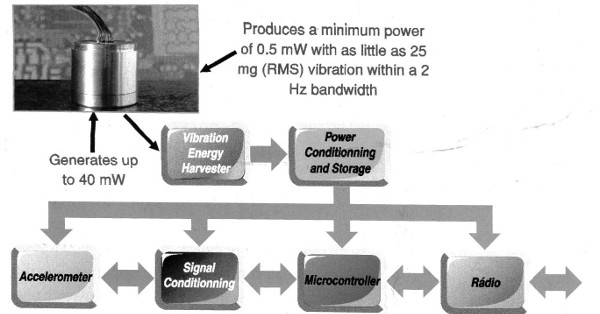
In applications involving short-distance data transmission with characteristics determined by the IEEE 802.11 standard, very small electrical power is required to power the transmitter circuits.
The idea of using energy from systems that produce vibrations, inherent in the equipment itself, is a good solution that eliminates the requirement of batteries and, therefore, the need for maintenance or monitoring of their condition. The use of piezoelectric generators such as those made by Perpetuum can be an excellent solution for many practical applications that fit in that context.