Note: This article is from 1982. Nowadays with the Arduinos and other control boards, it is possible to find servos of all types and sizes at very low costs.
Connecting relays, solenoids, or exhaust systems to radio control receivers allows reasonable work, but they are not the ideal solution.
In fact, with relays, solenoids and scape systems we do not have continuous control of the control positions, but rather a control by jumps which does not always lead the model to a realistic behavior like the one desired.
In the case of relays and solenoids, for example, we have only two possible control positions, as this device can only be switched on or off.
In the case of a car, boat or plane, being used at the rudder, we only have two possible control positions, which means that the maneuvers are abrupt (Figure 1).
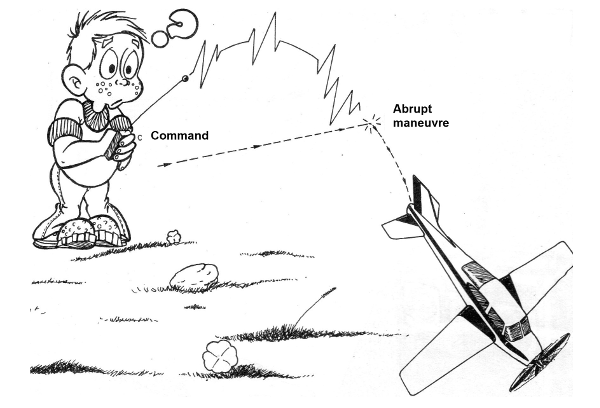
In the exhaust system, the situation improves somewhat because we already have intermediate positions, but the fact that the system can only act in one direction is an obstacle to control.
Note that the exhaust system only turns to one direction, which means that we can not move directly from one control position to the previous one.
We must first complete the entire actuation cycle to return to the initial position and then to the desired point. This is undoubtedly a problem for cases where rapid and precise maneuvers of the model are desired (Figure 2).
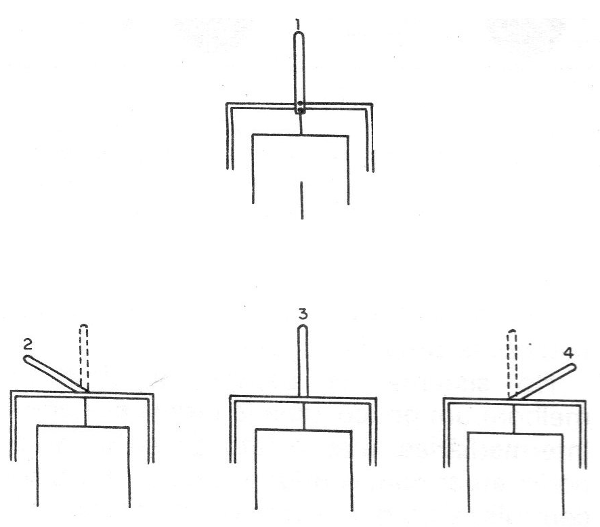
To obtain a linear control of a radio control system, devices called servos are used, which have already been described in other articles of this site.
These servos are small "motors" with reduction systems, which drive a lever or gear in a round trip and can stop in any intermediate position.
Coupled to the rudder of a boat, for example, they allow to obtain any desired position and a smooth transition from one to another, with much more realism for the model (Figure 3).
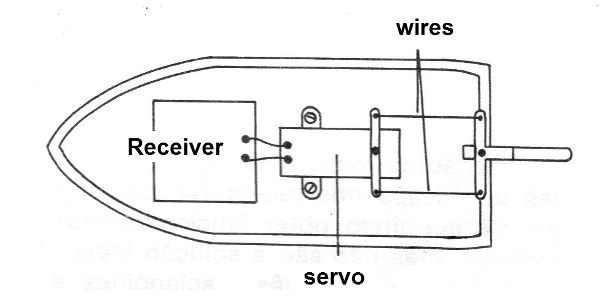
The servos, however, are not very accessible to our radio control setters. Since there is no domestic industry for these devices, the only way to obtain them is via importation (or the acquisition of new or used imported types in specialized houses), but its cost is not at all encouraging. (That at the time the article was written, today they are common.)
A servo will usually cost the assembler more than all the components used in the assembly of the radio control system (which are obtained in our trade), or even the model itself.
And, see that in order to have perfect control on an airplane, more than one servo must be used (Figure 4).
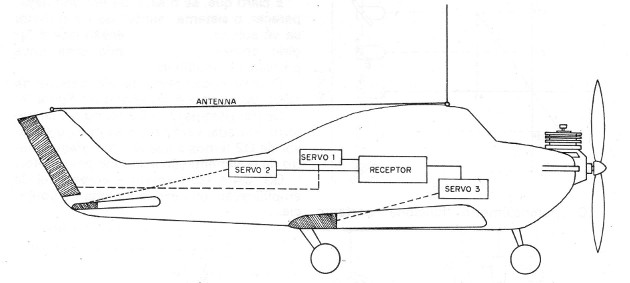
The assembly of a servi by the designer is also not a simple task.
Besides the somewhat critical electronic circuit that should occupy the minimum of space, we have the extremely delicate mechanical part which makes use of gears and parts, which must be totally built by the designer.
These pieces require the skill of a watchmaker and the availability of sophisticated tooling.
HOW IT WORKS
In Figure 5 we have the basic structure of a feedback or "closed loop" servo which is the most common type.
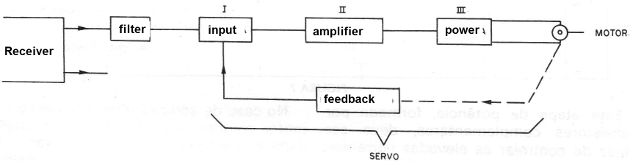
This servo has some operating drawbacks, even though it is the most popular, which is excessive current consumption, even when not triggered, and the difficulty in returning to the exact neutral position when it is pulled out.
In the circuit, we then have a transistorized input stage from which the control signal is removed from the receiver.
This control signal will be a voltage "proportional" to the desired movement, i.e., a voltage ranging from 0,25 to 1 V positive and 0,25 and 1 V negative, depending on the case (Figure 6).
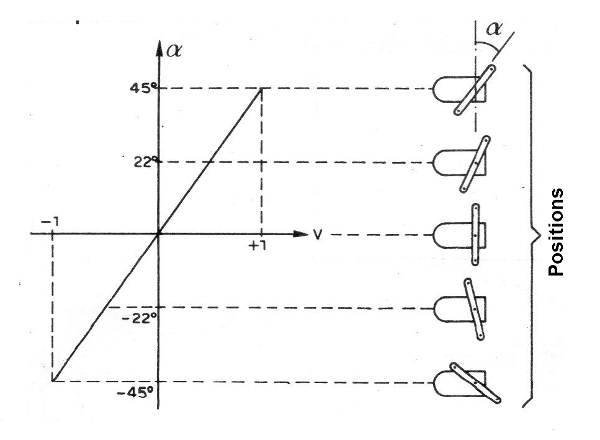
The movement will be proportional to this tension.
This voltage is amplified and taken to the second stage of the diagram, which is the power step, for driving a motor.
The direction of the rotation of the motor will depend on the polarity of the amplified input voltage.
In the motor gear system there is a small potentiometer whose purpose is to sense the position of the servo.
Thus, if the servo is in the center position (0 V input) and apply a signal which takes it to half its movement, 0.5 V, for example, what happens is: as the system moves, the potentiometer is also actuated so as to reduce the voltage applied to the motor as it approaches the desired position.
Thus, upon reaching the desired point, the voltage is reduced to zero in the motor and it stops.
The potentiometer acts as a "feedback loop", which allows to obtain any position for the servo, depending on the voltage of the applied signal.
Of course, if the input signal disappears, the system senses it, and the motor is subjected to a voltage which makes it turns again looking for a new position of balance.
The complete circuit of such a servo system is shown in Figure 7.
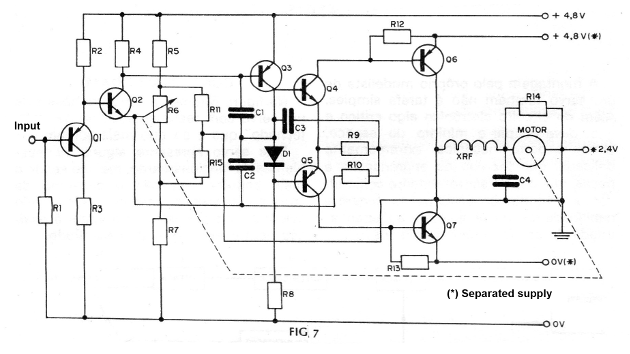
The transistors Q1 and Q2 form the input circuit, verifying that in the emitter of Q2 we have the connection of the feedback potentiometer driven by the motor. Q3, Q4 and Q5 form the final stage of amplification, which drives the power stage.
This power stage, made up of complementary transistors, must be able to control the high servo currents, which reach 500 mA or more, depending on the case.
As it is a circuit that works only as an example of operation we do not give the values of the components.
Note that the source used should be 4.8 V symmetrical for this case.
PROBLEMS WITH THIS SYSTEM
The most delicate part of the servo system with feedback by potentiometer is the potentiometer itself, which is subjected to the wearing of the resistive element or abnormal operation by the accumulation of dirt.
In the case of aeromodels, the vibration of the motor contributes to easily damage this element of the circuit, leading in a short time to an abnormal operation.
Frequent cleaning or even periodic replacement of this component should be done to ensure perfect servo operation.
In modern systems, these servos can be operated more reliably, with their replacement by a variable capacitor.
The position sensor then consists of a digital circuit operating by frequency and not by variation of resistance. Of course, in these cases we have a greater complexity for the system.