The motors are transducers which convert electrical energy into mechanical energy. In this function, they are part of a large amount of equipment that we find on a daily basis.
In recent times with the increasing union of electronics to mechanics with the creation of mechatronic devices, the engines appear in more and more quantity and in a variety of types not seen so far.
How the various types of engines that we find in the devices of our daily work and how to work with them is something that every professional needs to know and this is what we are going to talk about in this article.
DC Motor with Brushes
This type of engine is the most traditional known as "brush DC motor", to designate the operation with the commutator system.
In Figure 1 we have the cut view of an engine of this type, like the many found in common applications such as toys, car fans, etc.
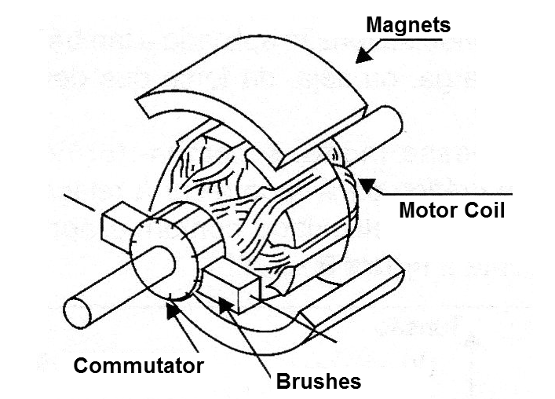
Note that permanent magnets are used in the stator, that the rotor where the coil is wound is made of ferrous metal to concentrate the lines of force of the magnetic field created by the coil, making it coarser and that the brushes are made of either pieces of Graphite or copper foils, depending on the type.
Motors of this type can be found in versions of all sizes and types, the most common being those supplied by batteries in the range from 1.5 to 12 V as shown in Figure 2.
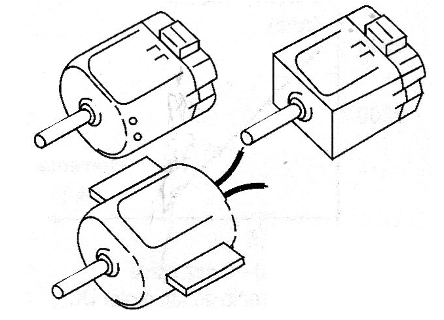
These small motors can operate with power of a few watts, since the drained currents typically vary between 50 mA and 2 A.
Features:
Engines of this type are actually specified to operate within a range of voltages. So a 3 V motor will actually work when fed with voltages in the range of 1.5 to 4.5 V without problems.
Above this voltage the major problem is the dissipation of heat by the winding.
Heating the wires too much can have their insulation burned since they are of the enameled type.
The speed of rotation of this type of motor depends on the voltage applied and also the load, that is, the force that must be done.
Small motors in the range from 1.5 to 12 V can have unladen rotations in the range from 1 000 to 10 000 rpm.
When charged, the current increases and the rotation drops, as shown in this chapter before.
For this reason, in a practical application it is necessary to specify both the applied voltage and the load so that one can have the exact idea of ??the rotation in which it is going to work.
In the most critical applications where the engine needs to maintain a constant rotation there are several techniques that can be employed for this purpose.
One of them is the mechanical speed regulation which can be achieved with counterweights as shown in Figure 3.
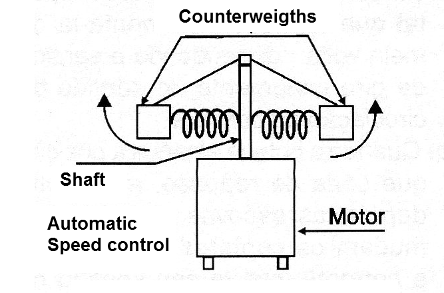
This adjustment operates so as to increase the speed, the weights move away from the axis of rotation and with this it is necessary a greater force to keep them in rotation compensating in this way the gain of speed.
Another possibility is the electronic regulation that can employ several practical configurations.
One of them is the use of some kind of regulator circuit of current or constant current source, as shown in Figure 4.
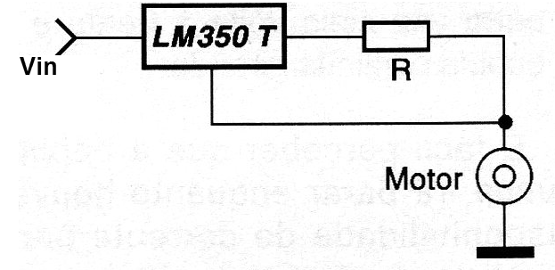
This circuit is used when the engine must engage a load with a constant force and keep the speed within certain limits.
It is understood that the current depends on the load and the rotation and once adjusted, a change in speed tends to modify the current that is compensated by the circuit.
Another possibility is the use of some type of sensor coupled to the axis of the engine which reads its rotation, as shown in Figure 5.
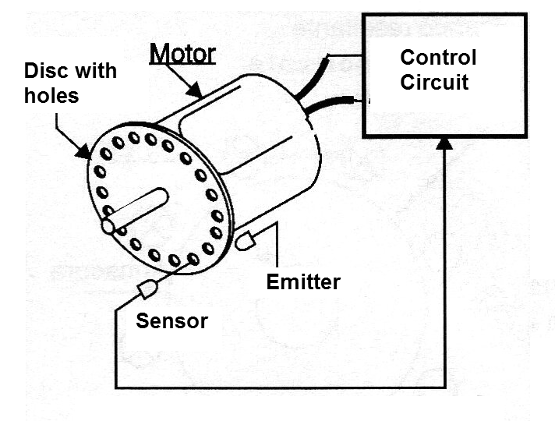
A magnetic or even optical sensor informs to the circuit which is the rotation and compares it to the set value generating an error signal. This signal is used to increase or decrease the voltage into the motor, thus correcting the speed until it reaches the desired value.
This type of motor has several limitations such as:
a) The maximum speed is limited both by the mechanical characteristics of the brushes and also by the core. At high rotations, the current reverses over and over thousands of times per second thus generating eddy currents in the ferrous core of the motor. This current makes the core heat up causing the engine to drop its performance.
b) In the commutations it is generated electrical noise that can interfere in the most sensitive circuits of the device in which the engine works. Although filters can be used to eliminate these noises, such as capacitors in parallel, there is a limit to their action.
c) The brushes or contacts wear out over time reducing the engine lifetime.
Several technologies enable the construction of DC motors with brushes of higher efficiency.
One of them is the one that has an engraved disk-shaped armature and that is shown in Figure 6.

This type of motor does not have moving parts of iron which eliminates the problems of the heating of the core in the high rotations by the currents of turbulence or eddy generated by the high frequencies.
In Figure 7 we have another type of DC motor that has a shell-shaped armature.
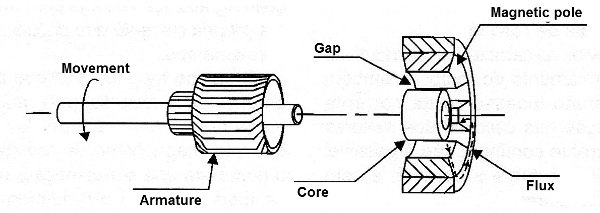
The great advantage of these engines over the traditional ones is that they can reach much higher rotations.
Losses in DC Motors
The basic purpose of an engine is to convert electrical energy into mechanical energy. Evidently, the best engine is the one that can convert most of the electrical energy into mechanical energy, that is, it has the highest efficiency or the lowest losses.
The losses in the motors of direct current, besides those already discussed in the previous item can have several other origins.
a) Losses in the windings
These losses occur because the wire used in the windings of the motors have some electrical resistance. To overcome this resistance, electric energy is converted into heat and not into mechanical force.
The losses by the winding resistance can be calculated by the expression:
P = R x I2
Where:
P is the electrical power lost - transformed into heat (W)
R is the winding resistance (ohms)
I is the current of the motor
An important factor that must be taken into account in these losses is that the winding resistance increases when it heats up, that is, when the motor starts to run in a higher power regime.
b) Losses by contact
The brushes do not allow a perfect electrical contact when the motor rotates. In fact, the efficiency of this type of contact decreases greatly as the engine speed increases.
As the contact efficiency decreases, the resistance increases and thus the amount of heat that is generated at this point in the motor.
The analysis of the way the contacts work is quite complex since there is the problem of the peak that generates transient pulses when they switch a highly inductive load such as the winding of the motor.
Instead of the simple establishment of the current we have the production of a sequence of very fast pulses which, acting on the inductance of the motor, make the established current not to immediately reach the expected value and in addition generate a higher return voltage.
c) Losses in the iron
The magnetization characteristics of the iron used as the core in the motors must be considered when analyzing the operation of a direct current motor with brushes.
The main one is due to the turbulence or eddy currents that are generated due to the hysteresis of the material used in the core.
As this material can not keep up with very fast reversals of polarity of the magnetic field when the motor spins at high speed, currents are induced in the core heating it up.
This heating may influence the winding resistance (as we have seen) and also the magnetic characteristics of the material used in the motor core.
In short, higher speed for this type of motor can mean considerable losses by the currents induced in this way. The use of metal plates instead of solid cores reduces the problem but does not eliminate it completely.
d) Losses by friction
These losses are due to the mechanical characteristics of the motor which must rotate on bearings with the least possible friction. Of course, in practice we can not reduce this friction to zero and losses occur.
The mechanical pressure of the brushes on the contacts in the motor rotor also induces frictional losses which, in addition to the inconvenience of acting as a brake, also generates heat which, as we have seen, is one of the factors causing a loss on the performance for this type of motor.
Materials such as graphite, which, in addition to being good electric conductors, have a very low coefficient of friction, are very helpful in obtaining motors with low friction losses from the contacts, but they are not totally eliminated and should be considered in certain applications more critical.
e) Losses by Short Circuit
When the brushes change contact from one winding to another in the rotation of a motor, for a fraction of second, the contact occurs in two windings at the same time, as shown in Figure 8.
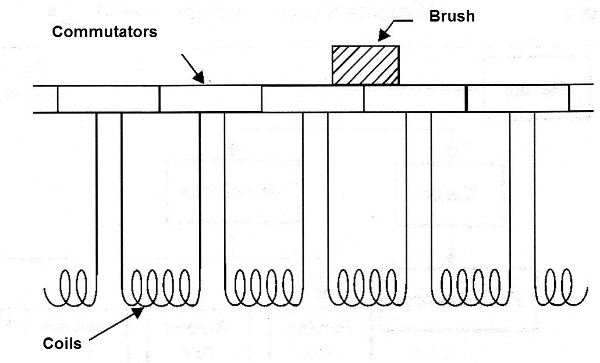
At the moment we have a short circuit that absorbs energy by converting it into heat.
Another problem that this short causes is to act as an electro-dynamic brake since the spirals are momentarily shorted thus generating a load for the motor.
Other Losses:
In addition to the causes analyzed there are others that affect the performance of DC motors which make use of brushes. Let's look at some of them.
a) Ripple of Torque
Due to the inductive characteristics of the motor winding and also due to the constantly inversion of the current by the action on the brushes of the DC motors it is not possible to maintain constant the current and with that the torque.
In practice, the torque varies according to a ripple curve that is shown in Figure 9.
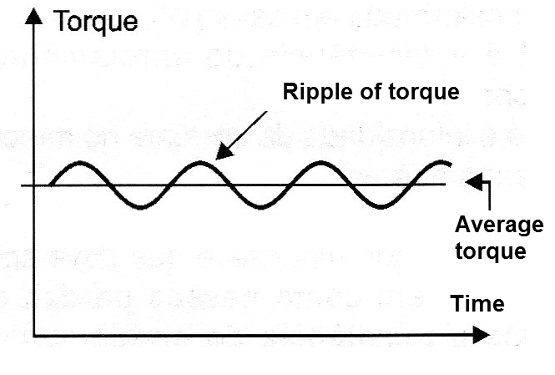
This characteristic usually causes problems of operation mainly at high speeds and can be minimized with the use of multiple windings in the motor or even increasing the number of commuting poles, but this certainly makes the device more expensive.
Other techniques may be employed to minimize this type of problem.
b) Demagnetization
The permanent magnets used into DC motors to create the field on which their operation is based are not so permanent, thus losing their magnetism over time.
Another factor that has an influence on the demagnetization of the permanent magnet is the very current that flows through the windings.
The magnetic field created by the windings acts on the permanent magnet and over time causes its magnetism to reduce to the point where it begins to affect in a sensitive way the performance of the motor.
It is important to note that a current intensity above a certain value in the motor windings can create a field strong enough to completely demagnetize the permanent magnets.
Thus, pulses of intense currents should be avoided anyway, because they can cause this type of problem.
c) Mechanical Resonance
All bodies tend to vibrate with greater intensity at certain frequencies and this is valid for the mechanical parts of an engine.
Thus, if we let a DC motor rotate freely without load it tends to accommodate itself in a rotation in which its mechanical parts oscillate at their resonant frequency.
At this frequency, mechanical stresses may appear which can both affect the integrity of the engine and its performance.
In practice, we use parts that have very different frequencies of resonance and even spin in opposite directions for this effect to be canceled.
d) Induced counter - EFM or CEFM
The fast commutation of the brushes from an inductive load causes an induced voltage to arise which is known as a counter-electromotive force.
In Figure 10 we show the characteristic of this force with the speed of rotation of a common motor.
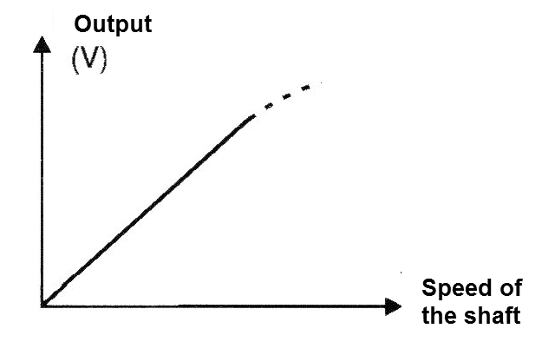
Note that this counter-electromotive force increases with the motor rotation speed. Usually for common engines it is expressed for a rotation of 1000 rpm.
This force makes the motor function as a generator that "returns" part of the energy to the circuit which feeds it acting as a kind of brake.
Brushless Motors
As we have seen, the greatest limitation for the operation of DC motors is the need to adopt a mechanical commutator system which reverses the current over and over during the movement in order to maintain the forces acting in the same direction to obtain a continuous rotation.
These brushes wear out, generate noise and are subjected to contact problems that worsen as the rotations increase.
The terminology used specifies brushless motors as a special type of servomotor. This observation must be made, because stepper motors are also brushless motors in the same way as an alternating current induction motor.
In the category of brushless motors we have two basic types: the trapezoidal motor and the motors for sine waves.
The trapezoidal motor is actually a DC servo while the sine is similar to a synchronous AC motor.
To better understand how they work we will start from the evolution of brushless motors.
A conventional brush motor, as shown in Figure 11, consists of a rotor with a coil which cut a magnetic field produced by the stator. If the coil connections are made through sliding rings, this motor behaves like a stepper motor (by reversing the current the rotor rotates 180 degrees).
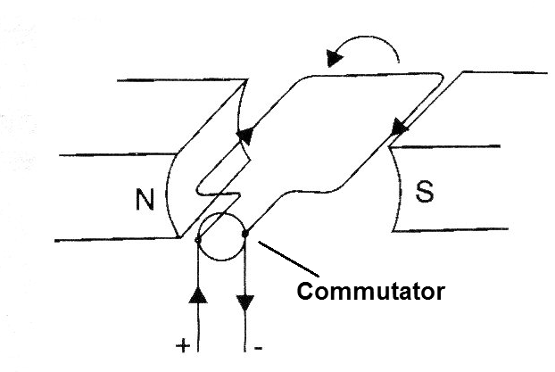
Including the commutator and brushes the current reversal will be done automatically and the rotor will continue to rotate in the same direction.
We must start from the elimination of the rotor windings to transform this motor into a brushless motor. This can be achieved by turning the engine "inside out". In other words, we put the permanent magnet as a rotating part of the engine and we put the coils in the stator poles.
Evidently, we still need to think of some way of automatically reverse the current - a switch triggered by a bounce could be used for this purpose as shown in Figure 12.
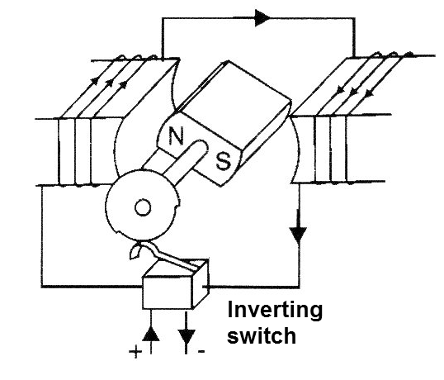
Of course, an arrangement that still includes a mechanical switching device is not the best solution for this problem.
Instead of the mechanical switch we can use an amplifier to drive the coils and which is driven by some device that can check the position of the rotor at each moment, for example, an optical sensor or a Hall Effect sensor, as shown in the Figure 13.
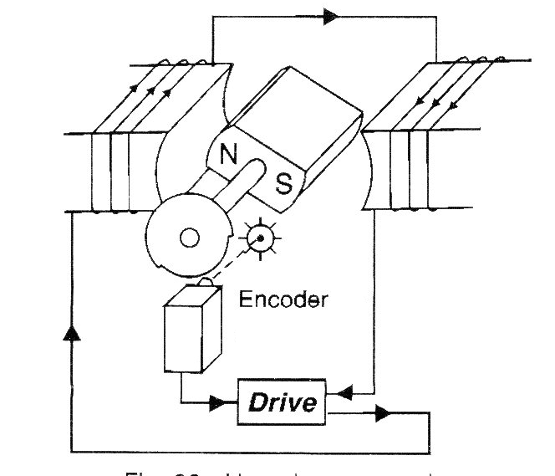
This circuit of reading the position and triggering the coils is called "commutation encoder" in technical language.
It is clear that an engine of this type cannot be connected directly to a direct current source to operate.
The motor must be connected to a circuit that constantly inverts the current, which ultimately means that the motor is activated by an alternating current.
Looking at the common brush motors, we see that a rotor that has only one coil has a feature of great variation of torque with the rotation.
In fact, the characteristic will be sinusoidal with the maximum torque since the rotor cuts the magnetic field in a way that results in this pattern, as shown in Figure 14.
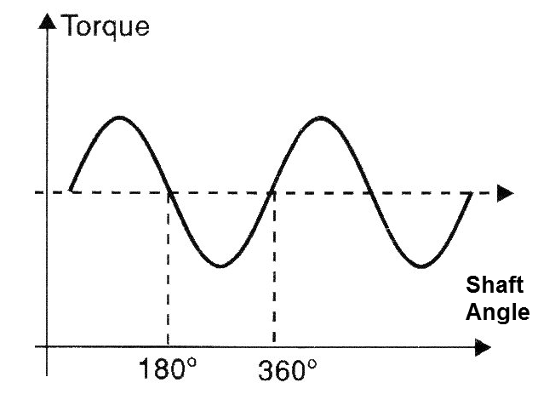
A DC motor in practice has several coils in the rotor and each one is connected not only to its own pair of switchers but also to other coils. In this way, we have a more constant torque by the effect of the average of the current circulating through them.
How to get the same behavior for a brushless motor? This will require a large number of coils in the stator, which in principle is not difficult to achieve, but it has the added disadvantage that we need a driver circuit for each of them.
In practice a brushless motor has two or three sets of coils or "phases" as shown in Figure 15.
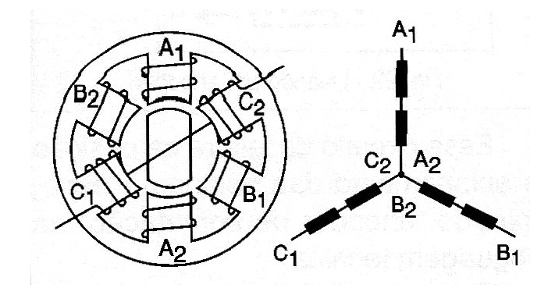
The motor shown in the figure has two poles and three phases. The rotor normally has four or six poles with a corresponding increase in the number of poles from the stator.
Note that this does not increase the number of phases because they can be distributed among several stators.
The torque features of this type of motor is shown in Figure 16.
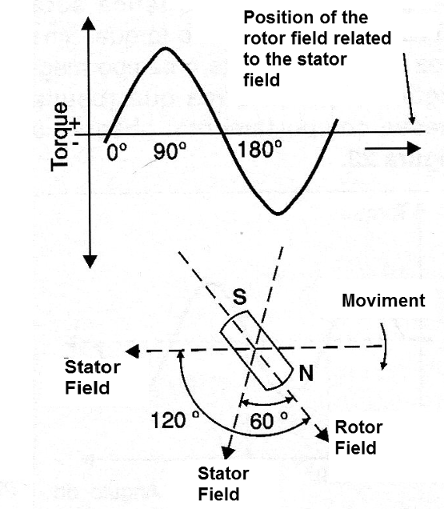
Through this figure we can see that the maximum torque is achieved when the stator fields and rotor are with a 90 degree lag.
By limiting the number of phases to three means that one can advance the stator field only in 60 degree increasings of the axis rotation, which means that this phase difference of 90 degrees can not be maintained.
In practice what is done is to maintain this difference oscillating between 60 and 120 degrees, so that on an average we will have 90 degrees with which a good approximation of the condition of greater torque is obtained.
The Trapezoidal Motor
With a fixed current intensity in the windings, a good increase of the torque can be achieved.
This results in a flattening of its torque characteristic shown in Figure 17, which by its shape gives the name to this type of motor.
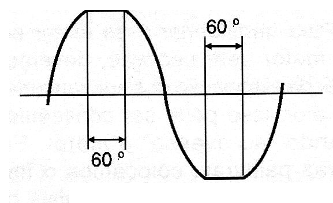
In practice this is not very simple, since a certain degree of non-linearity always remains. The main effect is a small "punch" at the commuting point of the circuit, which can be important in very low-speed applications.
The wave or wave of torque,resulting from this characteristic tends to produce some sort of speed modulation in the load. However, in a system that uses high gain speed feedback, the problem is eliminated. That means a small increase in speed generates a large error signal, reducing the torque demand to correct the speed.
In practice, the amplifier current tends to be a mirror of the torque characteristic resulting in very small velocity modulation as shown in Figure 18.
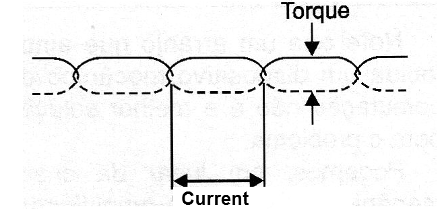
The Sinusoidal Motor
In the sinusoidal motor which is also called the brushless AC servo, no care is taken to correct the basic sinusoidal torque characteristics.
This engine can be powered as a synchronized AC motor by simply applying to the windings a sinusoidal voltage with the appropriate phase shift, 120 degrees in this case of three phase motors.
If a low speed accuracy is required, a higher stress accuracy should be achieved. This means that the drive must generate three currents which are in phase according to the axis position. To obtain the necessary precision in this coding, optical coders are usually used.
Constant Torque
To better understand how constant torque of this type of motor can be obtained, we had better analyze a case where we have only two phases.
This motor has two sets of coils that are fed with a trapezoidal signal lagged 90 degrees, one related to the other.
If we represent the position of the axis by an angle x, the currents in the windings will be in this form:
I = Io sen x
I = Io cos x
Looking at the basic engine model, we can observe that the fundamental torque characteristic of the motor is also sinusoidal, which means that the instantaneous torque will be given by:
T1 = Io K sen x
Where k is the engine torque constant.
Giving the current in the sinusoidal motor, and in phase with the characteristics of torque of the motor, the obtained torque of one of the phases will be:
T1 = (Io sen x) K sen x = I K sen2 x
And, in the same way, the obtained torque will be given by:
T1 = Io K cos2 x
The total torque obtained (in the two phases) will then be:
T1 + T2 = Io K (sen2 x + cos2 x)
But:
sen2 x + cos2 x = 1
Where we get:
T1 + T2 = Io x k
Thus, for sinusoidal currents applied to the motor, the resulting torque will be independent from the axis position.
See, however, in order for this to happen, there must be precision in the application of these currents in the engine, which requires the use of an appropriate encoder to send the necessary information to the processing circuit that generates it.
Hybrid Servos
Regarding the principle of operation, the stepper motor and the brushless servo motor are similar.
Each has a rotating magnet system and a stator with wound coils.
The only difference is in the fact that they have different numbers of poles. There are only 3 pairs in the hybrid servo and up to 50 in the stepper motor.
Thus, for analysis purposes we can consider a hybrid servo as a simplified stepper motor.
Based on the same principles we can use a stepper motor as a servo, by simply adding some feedback capability, such as an optical encoder.
The hybrid name comes precisely from the fact that its construction is based on the principles of both common servos and stepper motors.
They are even called in some cases of "stepper servos".
In Figure 19 we have a cross-sectional view of this engine type.
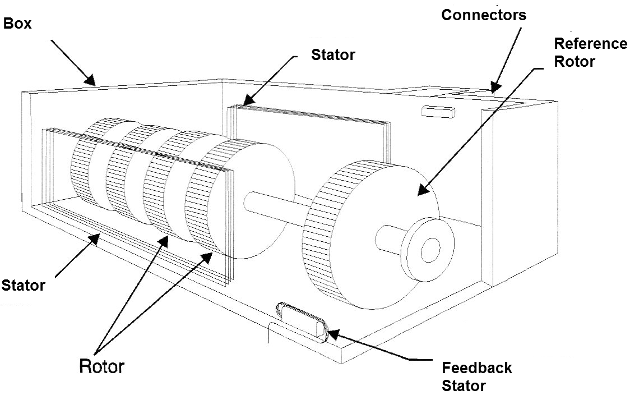
In this engine type a 2-phase drive provides the lagged currents (sine and cosine) which the windings need for the driving, always commanded by the feedback device. This device can be either an optical encoder or a contact sensor. As the motor has 50 pole pairs, 50 signal cycles must be generated for each spin of the shaft.
A hybrid servo has approximately the same torque of an equivalent stepper motor when fed by the same voltage and current, but it should be considered that the operation must always be in a closed loop.
A hybrid servo is more expensive than a stepper motor in a certain system, but cheaper than a brushless servo.
Continuous operation at high speeds is not recommended for stepper motors since many losses can occur in their core. Another advantage of this motor type is that it usually operates more quietly and heats less than ordinary stepper motors.
Direct Drive Motors
This type of motor is coupled directly to the loads which must move without the use of reduction boxes, gears or belts. In some applications brushless motors and even stepper motors may have a torque and resolution suitable for this application type.
In others, however, the reduction boxes and belts are used to modify the torque and speed according to the specifications required by the design.
An engine of this type has no brushes or gears for greater torque and higher resolution, while sacrificing speed and accuracy.
An important advantage of the direct driving is the elimination of friction and chafing of the gears which are responsible for significant power losses.
This type of motor contains precision components and a feedback system in a very compact housing.
The torque of this type of motor depends on its diameter and secondly on the number of teeth of which creates the magnetic field in order to obtain the greatest number of driving steps.
These motors have the main advantages of high precision, higher speed of response, higher torque at high speeds and smooth rotation.